Our services
Thermoforming Services
Plastic Thermoforming Services
Plastic Thermoforming is more common than you may think: synthetics are, in fact, the core element of a large part of common-use objects. Our company has been involved in plastic vacuum forming for decades, that’s why we can provide a quite pragmatic overview of plastic materials within the context of the thermoforming process.
We call plastics a wide range of materials based on polymers, which can be partly or fully synthetic.
CNC Machinery in the Thermoforming Process
The thermoforming process implies the need to cut and trim the formed shapes, for they appear as protruding surfaces of a flat sheet of plastic material.
The separation of the single formed pieces from the original plastic sheet can be operated manually, with a whipsaw and other cutting tools, or in a more rapid and precise way through the use of CNC machinery.
Mold Design and Production in the Thermoforming Process
Vacuum forming is a technology vastly applied in manufacturing several products and objects we are totally used to live among. So there’s plenty of different needs, features, and qualities to be considered.
Depending on the final item to produce (dimensions, materials, production quantity, etc.), it can be possible to go directly for the mold design, skipping the actual modeling step.
Models and Prototypes Manufacturing in the Thermoforming Process
The design of patterns, prototypes, and models represents the first step for any thermoforming production process. The model serves as a test for the ultimate mold, the one that will be used to shape the workpiece through vacuum forming: for it has to accurately reproduce the final piece, the design and the building of the mold is a crucial step in the economy of the whole manufacturing process. That’s why we often go for a temporary model before getting to actual production.
We can build models and molds up to 4800/2600/1200 mm, maintaining high-quality finishing standards.
Vacuum Thermoforming
Vacuum forming is an industrial process vastly used for plastic materials manufacturing: it is an extremely precise, effective, and cheap method compared with other industrial manufacturing processes.
Vacuum forming requires a plastic sheet to be heated and then applied to a mould — when it’s hot enough to be pliable. The application of vacuum suction completes the forming operation, making the sheet perfectly adhere to the mould surface.
Once the plastic is thoroughly cooled and stabilized, the vacuum formed sheet is separated from the mould.
Vacuum forming is one of the very few industrial processes which are fascinating and pleasant to look at. The generation of the workpiece is a completely visible process, thus the one standing at the molding machine attends some kind of “magic creation” every time the vacuum forms the final piece from the plastic sheet.
Vacuum forming is a molding technique widely used in several industrial processes, such as producing objects and components that are of daily use for most of us.
Before we go to the point, let us indulge in a brief digression, which may lead you somehow to appreciate the charming side of thermoforming.
Vacuum forming is one of the very few industrial processes which are fascinating and pleasant to look at. The generation of the workpiece is a completely visible process, thus the one standing at the molding machine attends some kind of “magic creation” every time the vacuum forms the final piece from the plastic sheet. Whereas the part of heating takes place inside the machine, in fact, the process of vacuum forming is carried out – from start to finish – under our eyes.
The vacuum forming process preserves a certain spectacularity even to used eyes: while the heating element moves back, the warm plastic sheet gets exposed. It gets slightly inflated and then leans on the mould, perfectly adhering to its surface. The plastic sheet movement, which replicates in a few seconds the mould surface as the air gets extracted, retains the charm of material transformation.
Thermoforming Process Technology
Back to the main topic, it’s useful to know that the vacuum forming process can suit several manufacturing needs. It’s a process that can be applied to various plastic materials with quite different technical features.
The most common materials we find in vacuum forming processes are ABS, PC /polycarbonate, PE/polyethylene, PP/polypropylene, PS/polystyrene, and PMMA/polymethylmethacrylate.
The plastic sheets themselves are cut in various thicknesses, according to the material, and the final product wanted features.
Vacuum forming presents several pros, such as:
- Machinery and equipment relatively low cost, which makes vacuum forming very suitable for the production of small and medium series;
- Good surface finishing, even without further adjustments;
- Ability to process remarkable size workpieces that allows proper freedom of design (max dimensions allowed is 2700×1500);
- Ability to perform the operations of cropping, trimming, and finishing both manually and using CNC machinery.
Compared to other molding techniques, vacuum forming allows high flexibility in production: it is possible, due to the speed and the efficiency of this manufacturing process, to produce different batches within a single order.
The vacuum forming charm reflects an excellent technical feature of the process: a plastic sheet through vacuum forming can perfectly adhere to any shape, generating almost any type of surface.
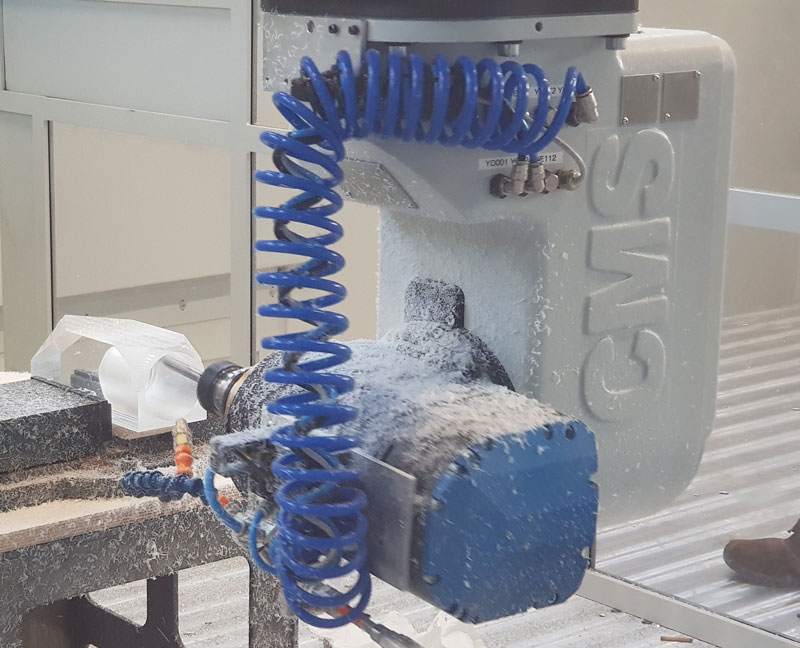
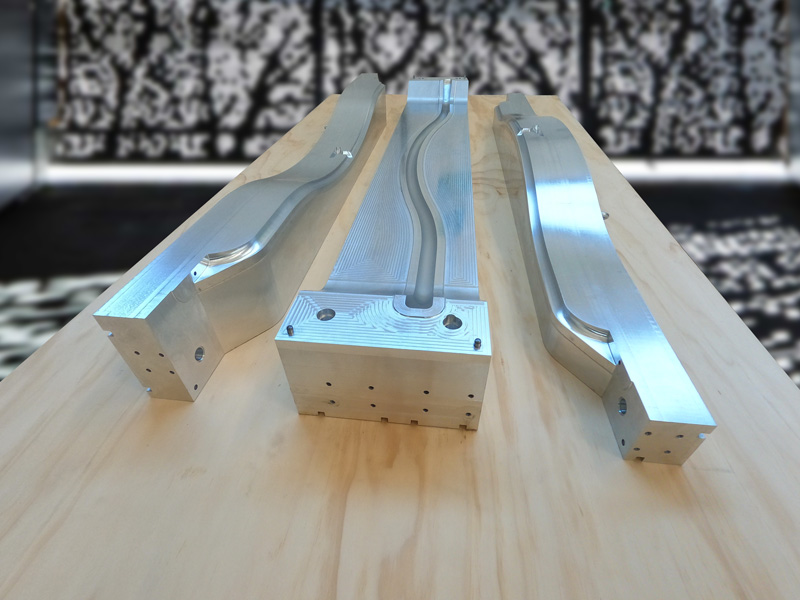
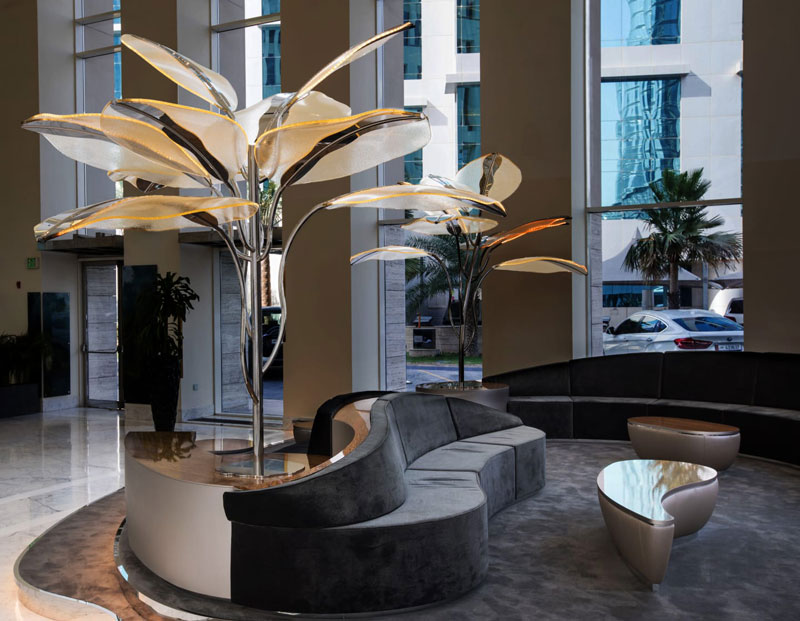
The uses of vacuum forming
If one were to ask which specific manufacturing sector more closely involves the vacuum forming technology, one would definitely have to mention the manufacturing of some products such as crankcases, machine tools, and cabinets canopies, bodyworks for tools and processing machines, bodyworks for small vehicles.
Vacuum forming and thermoforming are widely used in the automotive industry, such as in the manufacturing lines of machine tools and agricultural machinery. In particular, vacuum forming is often used for the production of internal paneling, car dashboards, and air conveyors.
We can find a lot of vacuum formed products in the furniture industry, too: trays, cabinets doors, chairs, sofas, tables, furnishing accessories, shower trays, coverages and canopies, components for household appliances can be produced through the vacuum forming molding process.
We are talking about a very flexible manufacturing system suitable for several applications, capable of handling production series from less than a hundred to thousands of pieces.
Our expertise
The vacuum forming process features, together with the familiar structure of our company, allow us to build a productive relationship with the client: cooperation and debate provide a working method that led our expertise over the years.
Our company is equipped with vacuum forming machines (of dimensions up to 2700×1500 mm) and 5-axis CNC trimming machinery. The factory has a specific area given to models and moulds manufacturing, which can rely on last-generation CNC machinery up to 4800x2600x1200 mm. Another specific sector is used as a mechanical workshop.
The experience acquired in the manufacturing of vacuum-formed ABS sheets allows us to offer clients the realization of complex products, such as those made up of several pieces assembled with glue or ultrasonic welding.