Thermoforming Our Specialty
Mold Design and Production in the Thermoforming Process
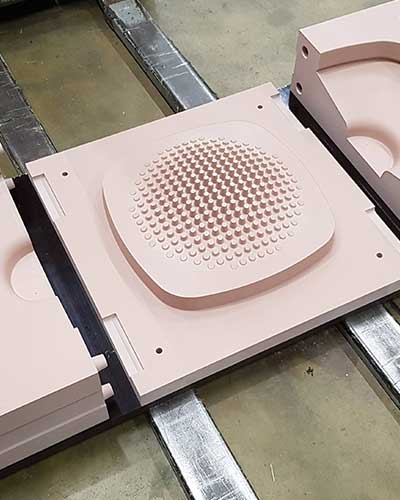
Vacuum forming is a technology vastly applied in manufacturing several products and objects we are totally used to live among. So there’s plenty of different needs, features, and qualities to be considered.
Depending on the final item to produce (dimensions, materials, production quantity, etc.), it can be possible to go directly for the mold design, skipping the actual modeling step.
The direct implementation of molds allows, within the thermoforming process, a considerable time and costs saving: that is made possible due to the flexibility and the accuracy of CNC machinery CAD-CAM systems. Still, the design of molds typically represents the second step of the overall process of vacuum thermoforming.
In the case of the aluminum mold, the intermediate passage of the female mold is avoided as the initial wooden model (or other material) is used directly as a foundry model.
How to choose the right mold: materials
Once the final piece is determined and the wooden or metal model is built, it is necessary to make some print tests to check everything’s working as needed. During test operations, it is possible to make corrections and adjustments, such as measurement and vacuum accuracy tweaks.
When every single detail produces the wanted results, then we can proceed to the definitive mold building for the actual serial production. The mold material is generally determined by the annual production estimated quantities. The most common options are aluminum or aluminum filled heat resistant epoxy resin (HDT).
The aluminum mold allows skipping the female mold step because it makes it possible to use the first wooden (or metal) prototype directly as a foundry model. Working with that model, the machine can process an aluminum cast that will present the workpiece’s ultimate shape. Aluminum castings are always processed on CNC machinery, which allows for better accuracy and finishing of the piece.
A valid alternative to aluminum casting is the production of the aluminum mold via direct CNC milling. Aluminum is a material that offers several pros, such as temperature maintenance through the whole thermoforming process.
When working with aluminum filled heat resistant epoxy resin, it is rather necessary to go for a female mold: the cast metal, in fact, has to be poured in the resin mold to become the ultimate production mold. The aluminum filling of the epoxy resin allows better durability and serves as a temperature transmitter, making control and temperature uniform distribution easier.
Machining the mold
The finished aluminum or resin mold must be mounted on a suitable plate to be processed by the machine. Both the aluminum and resin molds have to be provided with tiny holes, allocated on crucial processing points such as inner edges. This helps the whole plastic sheet follow the mold shape.
In the middle of the mold base plate, there’s the central air intake duct, which creates the vacuum within the mold: through the just mentioned tiny holes, the plastic sheet is forced to adhere to the mold surface, replicating its shape.
Each single series production needs a specific assessment, depending on the type of machine used, the given material, the features, and the workpiece’s dimensions.
Thermoforming Our specialty
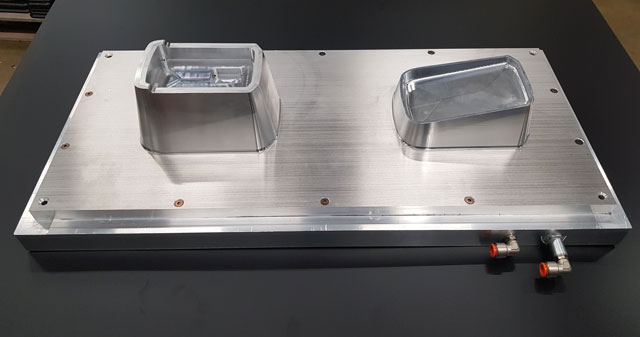
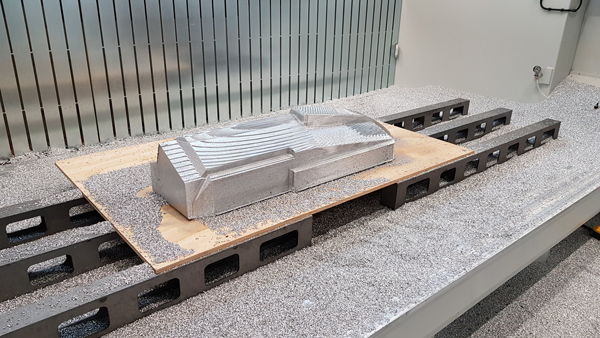
Expertise and customer care
Decades of experience in the industrial thermoforming process helped us come to a clear conclusion about mold production. To design an effective mold, we have to consider two basic requirements:
- The mold shall need a few printing tests before its finalization in order to lower production costs;
- The mold shall need little or no maintenance at all during the whole production process.
Both features depend on the craftsmanship, expertise, and technical ability of the workers employed to design and produce the thermoforming molds. Technology by itself, in fact, cannot replace the skills acquired from the direct experience of the process, such as creativity and problem-solving tips.
Our firm’s decades of expertise are the first guarantee for the complete satisfaction of clients’ needs. It allows us to process and meet the final product’s needs from the initial design to its ultimate development.